Laser Rust Removal Cleaning Machine Description:
The laser rust removal cleaning machine is assembled. It meets the cleaning requirements of complex shapes and fine positioning in the industrial processing field, and achieves higher cleanliness cleaning effects and lower overall cost production benefits.
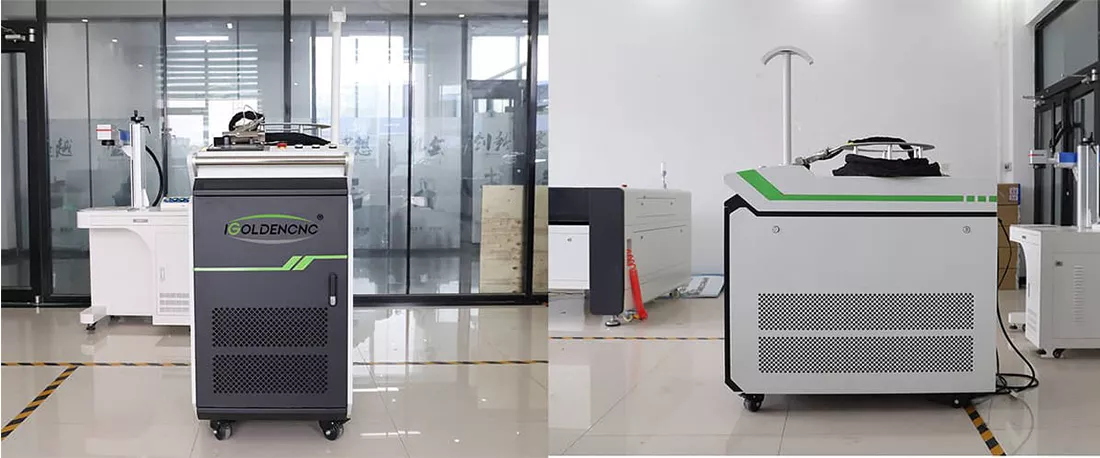
Handheld Fiber Laser Cleaning Machine Advantages:
- Supports process library storage.
- The system monitors the running status from time to time and monitors and collects the running status of lasers, chillers, and control panels.
- Temperature monitoring.
- Light weight, small size, ergonomic design, and comfortable grip.
- Safety lock.
- Easy to operate (small learning curve for operators) and can be hand-held or used with a robot to achieve automatic cleaning.
- Strong anti-interference.
- Fully sealed structure with built-in water and air paths.
- Configured with an independent research and development control system.
Rust Removal Laser Cleaning Machine Features:
- Non-contact cleaning (i.e., does not damage the substrate of the part).
- Can achieve selective cleaning of precise positions and sizes.
- No chemical cleaning fluid, no consumables, and safe and environmentally friendly.
- High cleaning efficiency (save time).
- The laser cleaning system is stable and requires almost no maintenance.
A few essential parameters to keep in mind:
Laser Wavelength | 1064nm |
Laser Power | 1000W/1500W/2000W |
Fiber Length | 8-10m(15m Optioned) |
Scanning Width | 10-80mm |
Voltage | 220V,50/60HZ |
Cooling Method | Water-cooling |
Working Temperature | 5-45℃ |
Cleaning machine laser head:
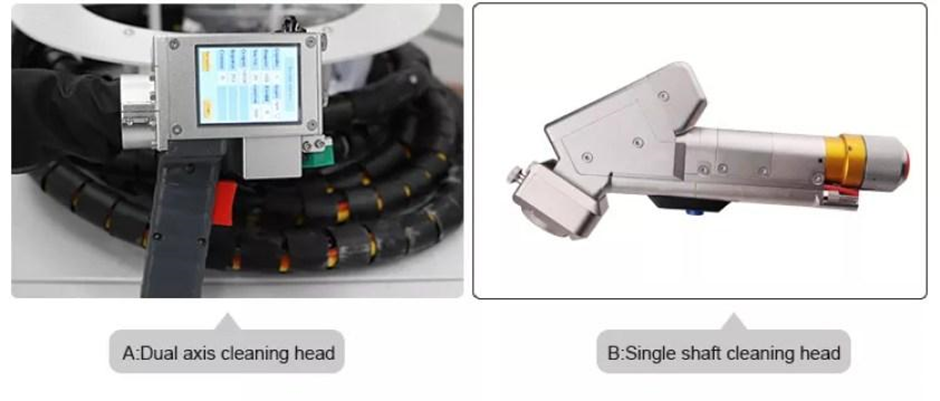
- High cleaning cleanliness It can accurately locate and clean contact cleaning, protect the surface of brittle materials, and effectively remove micron-level pollution particles; green and environmentally friendly, no consumables are required.
- This not only means that laser cleaning is effective, but the cleaning process is environmentally friendly.
- In addition, it does not use chemical cleaning agents, thus avoiding the damage caused by chemical corrosion to the material.
- The high-intensity light pulse generated by the laser that calculates and sets the threshold value forms an interaction between the short-pulse laser and the contaminated layer, resulting in a photophysical reaction.
- The beam is absorbed by the contaminated layer on the surface to be treated. The absorption of large energy forms a rapidly expanding plasma (highly ionized unstable gas), which generates shock waves.
- The shock waves turn pollutants, oxides, etc. into fragments and gases and are removed to complete the cleaning.
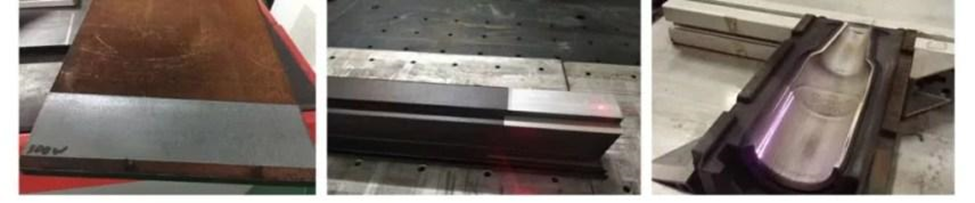
Laser Source
- The laser adopts water-cooled heat dissipation and rack-mounted chassis design.
- It has many advantages such as high electro-optical conversion efficiency, low energy consumption, compact structure, adjustment-free maintenance, and easy integration for customers.
- It is industrial laser welding and other Ideal light source for application.
S&A Chiller
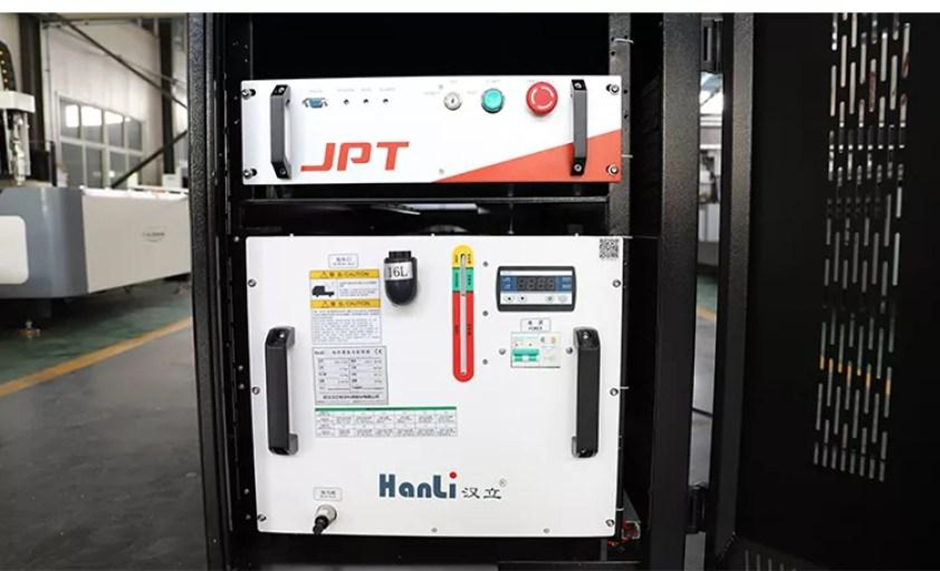
- The cooling capacity is up to 1400W, and environmentally friendly refrigerants can be used;
- Small size, long life and durable, easy to operate;
- The temperature control accuracy can reach ±0.3℃;
- The intelligent thermostat has two temperature control modes, which are suitable for different use occasions; it has a variety of settings and fault display functions;
- With multiple alarm protection functions.
Application Field
1. Rust removal from metal surface.
The laser cleaning machine has the following applications:
- Rust removal from metal surfaces.
- Paint removal from metal surfaces.
- Clad layer and coating removal.
- Oil fouling, blot, and dirt cleaning.
- Metal weld discoloration removal.
- Stone surface cleaning.
- Rubber mold damage-free cleaning.
Application Industry
The laser cleaning machine can be used in the following industries:
- Manufacturing plants
- Construction work
- Machinery repair shops
- Advertising
- Energy and mining
- Building material shops
- Ship industry
- Auto parts
- High-end machine manufacturing